Our circular economy expert Dr Jim Goddin attended the EU’s Raw Materials Week 2021. In this blog he reports back from the event. He explains how circular economy can help the EU resolve their raw materials crisis and reduce the materials challenges Australian and New Zealand businesses face too.
The EU faces major challenges
- How can it source the massive quantities of rare-earth metals like copper, aluminium, and magnesium it needs to generate low-carbon power, deliver electric transport at scale, and achieve its Net Zero carbon target by 2050?
- How can it minimise its exposure to disruption, price volatility and risk in the markets for critical materials?
- How can it produce critical materials sustainably – and become less dependent on imports from parts of the world where raw materials are produced in unsustainable ways?
Australian and New Zealand businesses face these challenges too
Many businesses Down Under trade heavily with the EU’s member states. Some are subsidiaries of EU companies or have subsidiaries of their own in Europe. Their global supply chains are increasingly connected. And like their European counterparts, they are moving to lower-carbon ways of working which rely on critical materials such as rare-earth metals.
Raw Materials Week 2021 / The International Round Table on Materials Criticality (IRTC)
In November 2021 European government representatives, miners, refiners, manufacturers, and recyclers met for the EU’s Raw Materials Week. The aim: to share knowledge and discuss the EU’s strategic direction. Minimising the EU’s exposure to market disruptions, price volatility, and risk was high on the agenda. The EU’s circular economy framework and trade policy featured too.
This year’s event took place at the same time as the meeting of the International Round Table on Materials Criticality (IRTC). Funded by the European Institute of Innovation and Technology, the IRTC brings together a diverse panel of global experts who specialise in critical materials. Sessions focused on how industry leaders are using circular economy principles and innovative technologies to reduce their supply risks. (Learn more in the last section of this blog).
Sourcing critical materials: why this matters
Critical materials have been a hot topic since 2009 when an export ban on rare earth metals from China affected many industries. China accounts for over 98% of the world’s supply of ‘rare earths’ – materials like dysprosium, samarium and neodymium.
Rare earth metals are vital components in the permanent magnets found in most electric vehicles and widespread in the miniature speakers and motors built into everyday electronics. They are also critically important in wind turbines: they allow gearboxes to be removed, making the turbines lighter and more reliable.
We’ve been here before – but it’s not the same
This challenge isn’t new, says Professor David Peck from the University of Delft. He points to examples from the Second World War, where disruptions to supply spurred innovation in materials.
However, times are different. Today’s technologies rely on far more elements in the periodic table than they ever did in the past. And while shortages of steel and rubber during the war led to innovation, these shortages were typically related to bulk materials.
Many critical materials today are minor alloying elements with particular (often unique) properties. Materials are far more specialised than in the past, and many materials in advanced technologies have no direct substitute. We’ve never produced many of these materials in the volumes we will soon need.
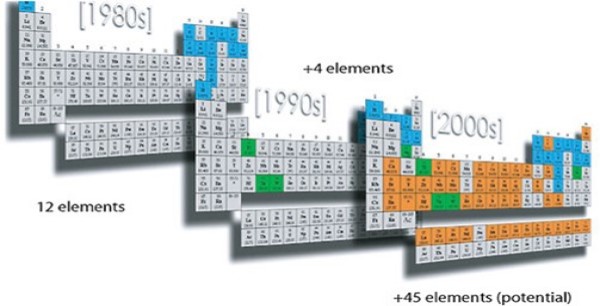
In just 20 years, as the electronics industry has grown, so too has the number of elements it uses: 12 in the 1980s, four more in the 1990s and a huge 45 more in the 2000s. (Source: Intel Corporation)
The EU’s list of critical materials has doubled in a decade
In 2011, the EU published its first list of critical materials. The list identified 14 materials, mainly metals, that were economically important to EU industries and increasingly at risk of disrupted supply. This list informed government policy, particularly domestic investment in production infrastructure and materials innovation. It also fed into trade policy with regions where these critical resources are concentrated.
The fourth and most recent version of this list, published in 2020, now includes 30 critical materials.
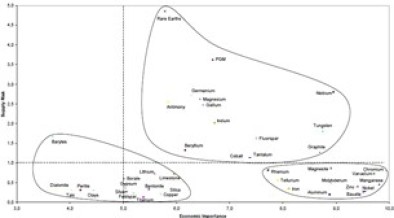
The EU’s critical materials list 2011 (top right: the most critical material; lower right: important materials, not at risk of disrupted supply) (Source: EU)
The EU’s dependence on imported critical materials 2020 assessment (Source: EU)
Why the EU needs to act: the example of magnesium
While its dependency on China for rare earths remains on the EU’s agenda of issues to resolve, it was magnesium that dominated discussion at the event, alongside the copper, lithium and graphite needed for batteries.
Magnesium is a vital element in many aluminium alloys. While aluminium is regularly recycled, some magnesium content is lost in the process, meaning it needs to be replaced with new material. Since the turn of the millennium, China has been steadily increasing its production of most light metals. It now produces 84% of the global supply of magnesium and over half of the world’s aluminium.
Production of magnesium by country of origin (Source: British Geological Survey and US Geological Survey)
Some people attending Raw Materials Week labelled the EU’s import dependence on these critical resources as ‘insane’. According to Rob Van Gils, CEO of HAI, the EU shed production of magnesium 20 to 30 years ago and now ‘has to beg China for access’.
One reason why the EU has moved away from producing raw materials is a prevailing public perception of mining as a dirty, low-value activity rather than a source of most of the technologies we enjoy today. There is undoubtedly a degree of mining ‘nimbyism’ (‘not in my back yard’ thinking) in most EU countries, and the barriers to approving new mines in the EU are significant. Moreover, many of the most desirable deposits in the EU are found in protected areas.
Still, the EU now appears resolved to reconcile protecting nature with needing to extract resources. It has also drawn a link between traditional coal mining regions in the EU and creating new mining activity for clean tech metals as part of a job retention strategy.
The EU’s action plan
The EU seems determined to excel in producing sustainably the materials it needs for a low-carbon economy. The European Commission’s Action Plan on Critical Raw Materials aims to develop resilient supply chains, strengthen domestic sourcing of raw materials in the EU, diversify sourcing from third-party countries, and reduce dependency on primary critical raw materials by using resources in a circular way. International collaboration underpins all these aims. These are some of the solutions it is working on.
Solution 1: circular economy
The link between critical materials and the circular economy has been apparent to some of us for most of the past decade. I started working on these fields simultaneously, and they were always inherently linked in my mind.
The EU’s action plan is the most assertive government communication we’ve seen linking criticality and circularity. One of the solutions to enhancing supply resilience for the EU is to transition to a circular economy to reduce demand for critical materials in absolute terms.
Metals producer Aurubis is taking a lead. They are using circular economy principles, including recycling, across their business and aim to become carbon-neutral well before 2050. Aurubis have increased the recycled content of their copper production. It now sits at 45%.
That said, experts recognise that recycling can’t deliver 100% of what the EU needs. So while, as circular economy practitioners, we could argue that reusing is a more effective circular solution than recycling, we should also recognise that we will continue to need a supply of virgin material for many years to come. Moreover, that supply resilience will depend on international collaboration and we will need to keep an eye on responsible sourcing.
Solution 2: responsible sourcing
Primary supply is essential for materials like lithium. We can’t source these materials from recycling in high enough volumes because we’ve never needed them in these volumes before. For these materials, trade policy seems set to dominate.
Anna-Michelle Asimakopoulou, a member of the European Parliament, indicated that the EU aims to be more assertive over trade policy with regions that can provide the materials they need. Denis Redonnet, the EU’s Deputy Director-General for Trade, echoed this view and highlighted that this would be particularly important for EU trade deals with Chile and Australia. Currently, the EU sources only 1% of its rapidly growing lithium demand domestically. The other 99% comes from these regions.
Solution 3: emerging technologies
The EU is looking to make greater use of emerging technologies. The European investment bank will increase finance for projects based on sustainable production, says Marcos Sefcovic, Vice President for Inter-institutional Relations and Foresight at the European Commission.
Solution 4: product passports
Mr Sefcovic also suggested that, as part of sustainable corporate governance, the EU will strengthen battery regulations by requiring every battery to have a publicly accessible digital passport detailing its carbon footprint, origin, and warranty. Using product passports signals to Original Equipment Manufacturers (OEMs – companies that produce parts and equipment, often used by other manufacturers) that manufacturing batteries sustainably is essential for the EU market.
Solution 5: insourcing mining in the EU
The EU appears more willing to adequately finance domestic mining to source the materials it needs in sustainable ways. In part, this resolve is due to realising that environmentally harmful and unsafe mining practices exist in some parts of the world due to the EU’s demand for low-cost raw materials. As the EU has outsourced producing its materials, it has offshored its impacts. It can no longer ignore this.
Examples from industry: circular economy and innovation
Disassembling IT devices recovers 10% of rare earth magnets
Dr Yasushi Harada from Hitachi Group gave an update on the company’s sustainability strategy. Hitachi’s approach, implemented five years ago, has already recovered 500 tons of used equipment, including 20,000 computer hard drives. Automated disassembly of devices has accelerated disassembly times. Hitachi now recovers 10% of their rare earth magnets. While sustainability drove Hitachi’s work, it has since proven economically viable as well.
Power-by-the-hour model increases performance and reliability
Dr Andrew Clifton from Rolls-Royce shared the challenges involved in substituting materials in the aerospace sector and the success of their Revert programme. The programme has seen vertical integration with suppliers recover production waste and exchange old material for new.
Rolls-Royce’s total care package sells engines at cost and charges a fixed rate per hour of use. This power-by-the-hour model is an example of the circular economy ‘product-as-a-service’ model. It has driven Rolls-Royce’s focus on high performance and reliability while making used parts more readily available. As a result, 50% of a Rolls-Royce engine is now a ‘closed-loop revert’ (materials return to Rolls Royce to be used again). The company is working on the remaining 50% of harder-to-recover materials.
Retaining ownership of metals reduces risk of price fluctuations
Christian Hagelueken of materials supplier Umicore shared the challenges of platinum group metals (PGMs). PGMs are on the EU’s critical materials list and have seen price volatility of 1,100% in the past three years (for rhodium). Price volatility has a significant impact on the cost of catalysts.
Umicore has started operating a split-price model which lets customers own the PGMs throughout the metals’ lifecycle. The model involves long-term contracts which require users to regenerate and recycle materials. Users benefit in several ways: there are significant cost savings, they are sheltered from volatile prices, and they can readily see how much material they are using.
Around 10% of materials are still lost from the system, meaning Umicore is still exposed to price fluctuations. However, these risks are much lower than in the past.
Product passports using blockchain provide data
Mesbah Sabur from Circularise and Nathan Williams from Minespider explained their blockchain-based product passport systems. Mesbah highlighted the lack of information available to recycling companies about the products they are dismantling. This lack of knowledge means companies waste time trying to recover materials that are not there.
Blockchain-based systems enable users to access the data buried in product supply chains. Both experts acknowledge that a mature system will need multiple solutions based on open infrastructure.
Mesbah shares my view that the circular economy will always be limited unless we have the correct data infrastructure to support it. Nathan highlighted that data providers often lack the incentive to populate the data needed. He highlighted the EU’s REACH regulations (Registration, Evaluation, Authorisation and Restriction of Chemicals), and suggests this regulation (and the mindset it encourages) has prepared most EU companies for the challenges involved in managing product data.
70% reduction in carbon emissions by recycling batteries
Hendy Kim from SungEel Hitech (a South Korean battery recycler) highlighted the problems involved in recycling batteries. These include the lack of standardisation from model to model even in the same make of vehicle. However, many car producers are jumping into battery recycling (alongside many new businesses), and he suggests there could be CO2 savings of as much as 70% for recycled lithium over mined lithium.
Reusing batteries in e-vehicles
Olivier Groux from Kyburz (an Austrian e-vehicle provider) shared their model for small electric vehicles. Batteries are recovered for reuse and end up in stationary systems (e.g. grid storage systems for electricity) before being recycled. The company’s approach relies on innovative manufacturing routes that enable very pure materials to be recovered when the battery’s anode and cathode are separated. They aim to recover battery-grade materials as they improve their technology.
Changing mobility and ownership models encourage battery reuse and recycling
Rajarshi Rakesh Sahai from Adaptive City Mobility (a German e-vehicle provider) highlighted changes in mobility and vehicle ownership. With many young people not wanting to own vehicles, he expects to see large city fleets of mass-market EVs with swappable batteries and easy-to-recycle materials. His business is also working on app-based access and mobility pooling, and stationary applications for electric vehicles.
New technologies harvest solar energy
Leah Charpentier from First Solar highlighted that we can’t meet our photovoltaic (PV) needs with today’s technology. Instead, we need to think about recycling. PV modules are predominantly glass, aluminium, and copper, but other materials represent the value. The 30-year design life of solar panels makes it challenging to justify investing in design to encourage recycling. First Solar’s thin-film technology aims to use fewer materials. It will start with by-products and each factory will have recycling facilities.
The company is recovering 90% of glass and 90% of semiconductor materials and achieving a forty-fold reuse of cadmium telluride. However, their factories are tied to recovering their products. Leah encourages specifiers and purchasers to include non-price criteria in tenders. These criteria should incentivise recoverable product designs and drive businesses to adopt circular economy principles.
January 2022