There is no waste in a circular economy, only resources and opportunities to use them to their full potential. Unlike a linear economy, a circular economy or ōhanga āmiomio, proposes a model in which economic growth is not connected to an increased use of limited, natural resources. Instead, growth in a circular economy relies on designing products and systems for longevity in their first life and recyclability and reusability for consequent lives. Therefore, we can keep resources in use for as long as possible and reduce the demand for raw (virgin) material — getting the most value out of existing materials and reducing the costs of material extraction methods in the process.
However, we currently live in a linear economy with a take-make-dispose model in which waste is inevitable. While there is still a way to go before we reach a truly circular economy, some businesses are leading the transition with innovative approaches to create value with waste-based products. From galvanising to paint to IT equipment waste, we look at some of the local businesses creating golden opportunities with waste.
Zincovery — Creating a waste free industry
The galvanised steel industry produces a waste acid with a high concentration of zinc — an eco-toxin that is essential for humans in trace amounts but toxic to aquatic life. Generally, this is disposed of via wastewater and landfill after treatment. However, this results in the loss of zinc, a useful mineral, and its incomplete removal from wastewater degrades most sewage treatment processes and causes environmental damage to waterways.
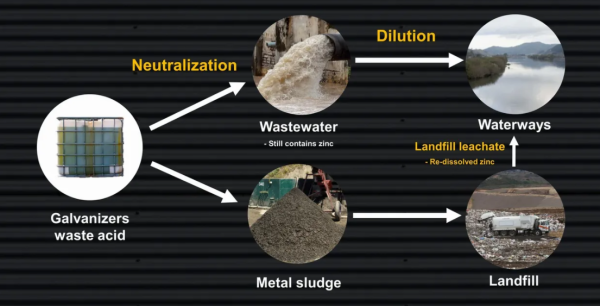
Image source: Zincovery
The galvanized steel industry produces a waste acid with high concentrations of dissolved zinc and iron. After neutralization, this is usually disposed of into wastewater and landfill. This treatment is inadequate because of the wastage of zinc and the incomplete removal of zinc from wastewater. Zinc causes environmental damage in waterways.
Zincovery tackles these issues by taking the waste acid and recycling it while also recovering zinc. While extracting valuable materials from waste is certainly circular economy friendly, it does not necessarily have to be climate friendly. Zincovery considers the climate impact of their processes with a carbon footprint, ensuring that they have the data required to make well-informed decisions that don’t cost the planet.
Avertana — Breathing life into waste
Avertana delivers on its vision to ‘breathe life’ into existing industrial waste by extracting valuable minerals and chemicals from waste that are used in the manufacture of everything from paint and paper to fertilisers. The process technology developer focuses on delivering circular economy solutions by taking low-value by-products from heavy manufacturing and turning them into commodities, without creating additional solid waste. James Obern, VP Commercial and Co-Founder of Avertana, explains the benefits: “Starting with a low-value raw material and turning it entirely into products gives our process a much lower manufacturing cost and also a far smaller environmental footprint than the take-make-dispose value chains we see today in the industries that our process serves.”
Avertana is well-positioned to tap into the increasing demand for sustainability in industrial supply chains. “Our discussions with major end-users of the products our process makes, from paint to water treatment chemicals to concrete, have confirmed they are strongly motivated to make their supply chains more sustainable,” says James.
Waste slag, a solid by-product of steel manufacturing, is the main area of focus for Avertana as it provides the raw material for their extraction technology. The idea for Avertana’s slag refining process originated from a desire to connect unavoidable industrial waste with large commodity markets.
Although the team had a good understanding of their technology’s potential impact on climate and the environment, they wanted to base their decisions on data rather than intuition. James explains why they undertook a Life Cycle Assessment (LCA) study: “We originally set out on the LCA journey because we wanted to measure how our process stacked up against the technology options already available to pigment manufacturers. While we intuitively understood that our solution should be greener, the LCA process allowed us to quantify the expected environmental advantages of our process at scale. The LCA enables us to be confident that what we are bringing to market is truly a better alternative to current pathways, not just for CO2 emissions but also solid and hazardous waste reduction.”
Mint Innovation — Turning waste into gold
Another local company is completely reconceptualising waste, turning e-waste — a significant area of waste in NZ — into gold. Mint Innovation has developed low-impact and low-cost technology that extracts gold and other precious metals from e-waste such as old laptops, computers, and mobile phones. The company is looking to work with local recyclers to collect e-waste, recover metals, and make them available for reuse in the manufacture of new products. The company has a pilot plant in Auckland and has recently announced an upcoming large-scale bio-refining facility in Sydney.
While Mint Innovation focuses on recovering precious materials from e-waste, the Government focuses on minimising the amount of e-waste that is being sent to the landfill. In July 2020, the Government announced six priority products including e-waste for regulated (mandatory) product stewardship under the Waste Minimisation Act. Product stewardship puts more responsibility for a product’s end-of-life on the people who create, import, sell, and use it, rather than on communities, councils, neighbourhoods, or nature. While regulated product stewardship is an important step to address waste, it is only part of the wider equation. Companies like Mint Innovation fill in the technology gap to progress from minimising waste to creating value out of waste.
Taking it one step further with cradle to cradle design
These companies transform waste into opportunities, keep resources in use for as long as possible, reduce the demand for virgin resources, and minimise waste. If we go back one step further and design products for a circular economy, we can make it easier and more cost-effective to extract materials at their end-of-life.
The ultimate circular product is one designed with cradle to cradle principles. Traditionally, products are designed for one life with a cradle to grave approach, with some being recycled and most being landfilled at the end of its useful life.
The Cradle to Cradle® (C2C) design principles established by Dr. Michael Braungart and William McDonough offer an alternative to keep materials in circulation with technical and biological spheres. All materials are considered nutrients in a cradle to cradle system and return to their respective spheres to be used again and again.
According to Cradle to Cradle®, there is no such thing as waste, only materials in the wrong place. Although C2C is built on circular principles, it employs a wider systems approach to ensure that it does not neglect the other impacts that can be caused by a product at any stage in its life cycle. This includes the working conditions of people in the supply chain and the carbon footprint of products.
A C2C certified product is designed with circular economy principles and created in alignment with high social and environmental standards. At the end of its life, a product made according to C2C principles is the best place to find waste as good as gold.
By Barbara Nebel and Femi Perumbally
This article was first published in NZ Manufacturer magazine, July 2021.