In the transition to a circular economy, New Zealand first needs to address its continued reliance on a linear take-make-waste model. For organisations looking to take meaningful action, taking responsibility for the end-of-life of their products with product stewardship can be a key part of the solution. With proponents ranging from successful businesses to new industry and governmental initiatives, it is safe to predict that product stewardship is here to stay and ready to play a pivotal role in the circular transition. Starting with the waste problem during this process is a common tactic but the best approach starts at the beginning with product design. In fact, UK based Waste and Resources Action Programme (WRAP) found that 80% of the environmental impacts of modern products are determined during product design and development. Incorporating product stewardship into product design will provide more circular solutions for end-of-life decisions, minimise waste in the process and ultimately, speed up the transition to a circular economy. This is exactly what Utility Electric Vehicle (UEV) company UBCO has set out to do.
Starting with product stewardship
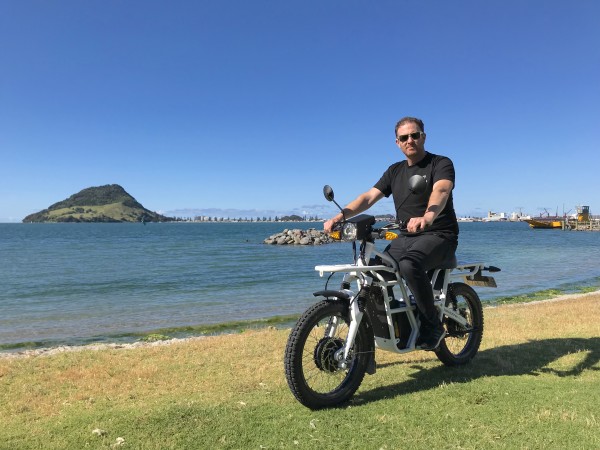
UBCO's Utility dual electric drive motor bike
Focused on a largely electronic product with a high capacity lithium-ion battery, UBCO identified end of life processes and product stewardship as their defining sustainability issues. For UBCO, tackling these issues head on starts with design.
UBCO’s product design approach utilises life cycle thinking to consider the entire value chain – from the raw materials and the energy used to create the product, through to the packaging, distribution, use, maintenance, and eventually recycling, reuse, recovery, and final disposal. “It would have been easiest to have battery and electronics in a big block of resin to make it waterproof – but that would prevent any product stewardship approach
in future”, says Timothy Allan, CEO and Managing Director of UBCO. UBCO’s aim is not to follow the easiest approach, rather it is to increase product durability, life span and recyclability for each generation of product with this process.
The full integration of vehicle, hardware, software, and communications helps the company to unpick the traditional model of selling bikes to develop a new subscription model. This enables customers to pay a monthly subscription for the bike or battery, while UBCO retain ownership and responsibility for the product and its end-of-life solutions. End-of-life solutions for batteries is exactly what the Battery Industry Group (B.I.G.), a promising new initiative is focused on.
‘Circular’ product stewardship
As the name suggests, B.I.G are concerned with large batteries including those used in EVs, other modes of transport such as planes, and energy storage. A tenet of the 140-member collective is the need for product stewardship to start at the design stage and be circular, hence its focus on involving the whole battery value chain as a multi-sector collaboration.
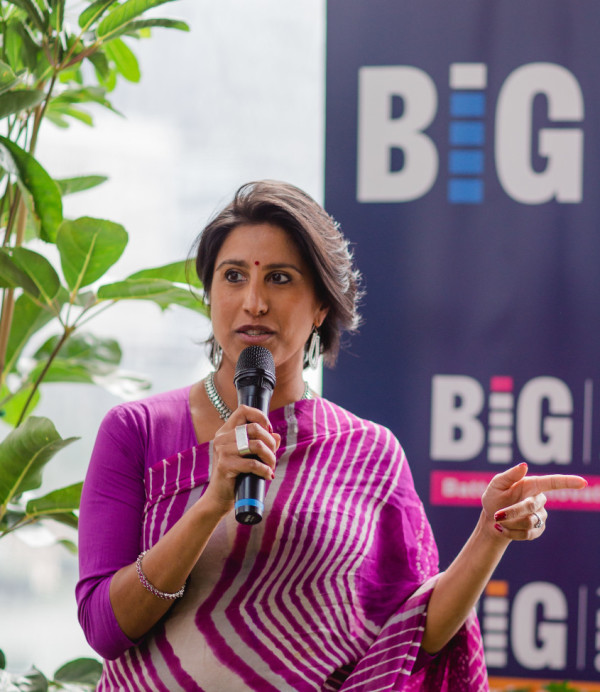
Juhi Shareef, Chair of the Battery Industry Group (B.I.G.)
Circular product stewardship requires materials and products to retain their highest value at every stage in their life cycle and for its life span to be extended as much as possible. In the case of batteries, this can take the form of ‘battery karma’ or reuse. “Battery karma denotes the fact that EV batteries have the potential for a second or even third life as stationary energy storage or other applications”, says Juhi Shareef, Chair of the Battery Industry Group (B.I.G.) in thinkstep-anz’s recent product stewardship webinar. For example, batteries taken out of an EV to be replaced, often have sufficient capacity to be reused, whether it is for a boat, a battery bank or in stationary energy storage. A key ingredient for lithium ion batteries, cobalt extraction presents a very real risk of exploitative labour including child labour. Therefore, B.I.G.’s focus on the reuse and eventual recycling of batteries will not only ease pressure on limited resources but will also reduce reliance on the risk laden aspects of its supply chain especially in the earlier stages such as cobalt extraction and mining.
Around 84,000 large batteries will reach their end-of-life by 2030. With an understanding of the volumes of large batteries requiring better end-of-life processes, the group is currently in the early stages of developing a ‘circular’ product stewardship scheme for large batteries. A scheme design to guide
the transformation for large batteries from a closed value chain to a circular value loop is expected to be completed in mid-2021. While both UBCO and B.I.G. demonstrate the promising initiatives taking place in the voluntary space, the next step as recently announced by the Government is mandatory product stewardship schemes.
Changing tides with regulation
The Ministry for Environment announced a major change for regulated product stewardship in July with mandatory schemes introduced for six high priority product areas under the Waste Minimisation Act. The products are plastic packaging, tyres, e-waste, agrichemicals and their containers, refrigerants, and farm plastics. The mandatory product stewardship schemes will tackle major sources of waste including e-waste by turning end-of-life solutions into an obligatory responsibility rather than a voluntary one. The newly introduced schemes shift the responsibility for a product’s waste management from communities, councils, neighbourhoods and nature to manufacturers, importers, retailers, and users. In other words, the responsibility shifts to groups with a direct connection to the product whether it is in the stages of creation, distribution, or use.
Getting started with product stewardship
Organisations with successful product stewardship schemes in place demonstrate that it is not only a viable option for the circular transition, but also an economically sound one. With product stewardship established in 2015, Fuji Xerox is among the companies that now come to the forefront as major sources of guidance. In 2019, the company’s product stewardship scheme was able to divert more than 925 tonnes of waste from landfill and save over $900,000 in the process.
The Fuji Xerox roadmap, based on the Ministry for the Environment’s accredited product stewardship scheme, provides a free step-by-step guide to help other businesses develop product stewardship schemes including how to design products for a circular economy. Product stewardship schemes will not only help to address NZ’s waste problem but will also ease some of the pressure on landfills and reduce associated emissions. Furthermore, it will help to extend the lifespan of existing materials and products, and consequently, reduce the demand for limited natural resources and associated supply chain and environmental risks. Starting with product design ensures that the solutions treat the cause of the problem and not just the symptoms.
By Barbara Nebel
This article was first published in NZ Manufacturer magazine, September 2020.